Recognizing Porosity in Welding: Discovering Causes, Impacts, and Prevention Methods
As professionals in the welding industry are well conscious, comprehending the reasons, results, and prevention methods associated to porosity is critical for accomplishing durable and trustworthy welds. By delving right into the root causes of porosity, analyzing its destructive effects on weld high quality, and exploring effective prevention approaches, welders can boost their understanding and abilities to produce high-quality welds regularly.
Typical Reasons For Porosity
Porosity in welding is primarily triggered by a combination of aspects such as contamination, incorrect securing, and inadequate gas protection during the welding procedure. Contamination, in the kind of dust, grease, or rust on the welding surface, produces gas pockets when warmed, causing porosity in the weld. Inappropriate shielding occurs when the securing gas, generally utilized in processes like MIG and TIG welding, is unable to totally shield the molten weld pool from reacting with the bordering air, resulting in gas entrapment and succeeding porosity. In addition, insufficient gas protection, typically due to wrong circulation prices or nozzle positioning, can leave parts of the weld vulnerable, allowing porosity to develop. These factors jointly contribute to the formation of gaps within the weld, deteriorating its integrity and possibly creating structural issues. Comprehending and addressing these typical reasons are vital steps in protecting against porosity and guaranteeing the top quality and strength of welded joints.
Impacts on Weld High Quality
The existence of porosity in a weld can significantly compromise the overall top quality and honesty of the bonded joint. Porosity within a weld produces spaces or tooth cavities that weaken the structure, making it more vulnerable to cracking, corrosion, and mechanical failing. These voids act as anxiety concentrators, lowering the load-bearing capacity of the weld and enhancing the possibility of early failure under used anxiety. In addition, porosity can additionally offer as potential websites for hydrogen entrapment, further intensifying the deterioration of the weld's mechanical residential or commercial properties.
Additionally, porosity can impede the effectiveness of non-destructive testing (NDT) techniques, making it testing to identify other flaws or interruptions within the weld. This can lead to considerable safety problems, especially in crucial applications where the architectural honesty of the welded components is extremely important.
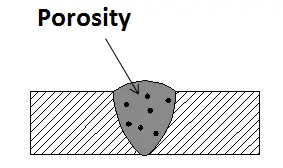
Prevention Techniques Summary
Given the detrimental influence of porosity on weld quality, efficient prevention techniques are crucial to keeping the structural stability of welded joints. Among the main avoidance techniques is extensive cleansing of the base products before welding. Contaminants such as oil, grease, corrosion, and dampness can contribute to porosity, so making certain a clean work surface area is important. Correct storage of welding consumables in completely dry problems is additionally critical to avoid moisture absorption, which can result in gas entrapment during welding. In addition, picking the appropriate welding specifications, such as voltage, current, and take a trip rate, can assist decrease the threat informative post of porosity formation. Making certain sufficient protecting gas circulation and coverage is one more essential avoidance strategy, as not enough gas insurance coverage can lead to climatic contamination and porosity. Proper welder training and certification are necessary for implementing preventive actions effectively and consistently. By including these prevention methods right right here into welding practices, the occurrence of porosity can be dramatically minimized, causing stronger and extra dependable welded joints.
Significance of Appropriate Shielding
Appropriate shielding in welding plays an essential role in stopping atmospheric contamination and making sure the honesty of bonded joints. Shielding gases, such as argon, helium, or a mixture of both, are commonly made use of to protect the weld swimming pool from reacting with elements in the air like oxygen and nitrogen. When these responsive elements enter call with the hot weld swimming pool, they can create porosity, bring about weak welds with decreased mechanical homes.
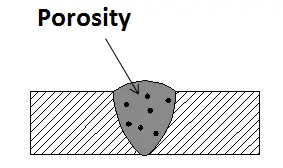
Insufficient protecting can cause numerous defects like porosity, spatter, and oxidation, jeopardizing the structural honesty of the bonded joint. Therefore, adhering to proper securing methods is necessary to create high-quality welds with very little flaws and guarantee the durability and dependability of the bonded parts (What is Porosity).
Tracking and Control Approaches
Exactly how can welders properly check and control the welding process to ensure ideal outcomes and protect against issues like porosity? By continuously keeping an eye on these variables, welders can determine inconsistencies from the ideal problems and make instant adjustments to protect against porosity formation.

Furthermore, implementing proper training programs for welders is important for checking and regulating the welding procedure effectively. What is Porosity. Enlightening welders on the value of keeping consistent specifications, such as proper gas shielding and travel speed, can aid avoid porosity issues. Regular analyses and certifications can additionally make certain that welders are efficient in tracking and controlling welding procedures
Additionally, using automated welding systems can improve monitoring and control abilities. These systems can precisely regulate welding specifications, lowering the possibility of human mistake and making sure consistent weld top quality. By combining sophisticated surveillance technologies, training programs, and automated systems, welders can effectively keep track of and regulate the welding process to decrease porosity flaws and achieve top notch welds.
Final Thought
